Improving Uptime & Efficiency in Coil Handling and Assembly with Precision Hoists
Products Provided
Rope Hoist and Crab Hoist - S/G & D/G EO Cranes
The Problems & Challenges
For a manufacturer of electrical steel laminations and motor cores, uninterrupted production was non-negotiable. They knew that once operations began, any downtime in coil handling or stamping would cost them both time and efficiency.
Rather than waiting for problems to arise, the client took a forward-thinking approach. During the building’s construction phase, they approached us to design and integrate a hoisting solution tailored to their future operations. Their goal was clear: no disruptions, no delays — just a seamless start to production.
They wanted a system that wouldn’t fail when production peaked. A setup that wouldn’t become a bottleneck. And above all, they wanted reliability from day one, so the team could focus on manufacturing, not maintenance.
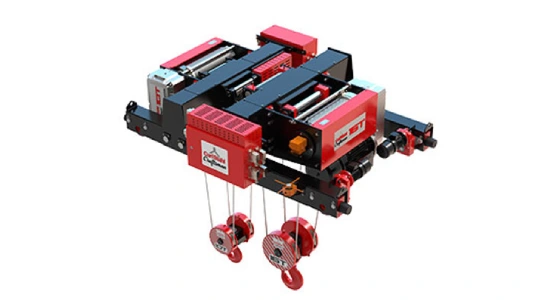
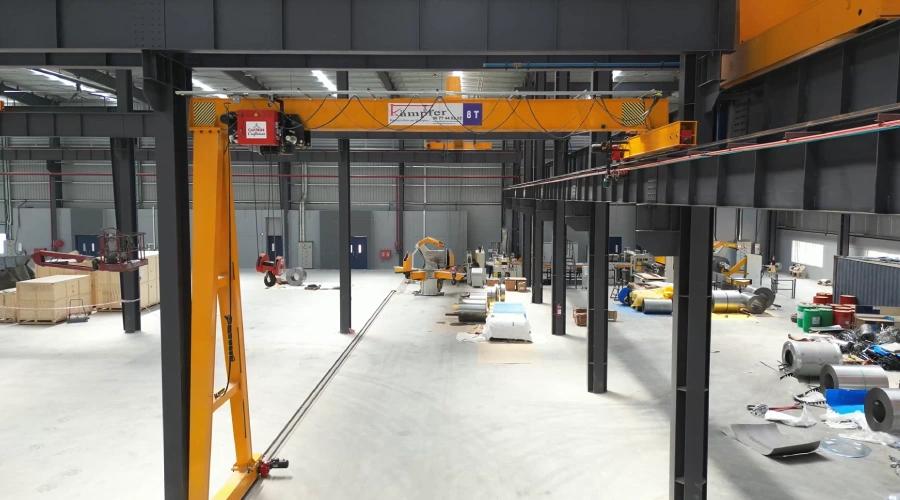
The Solution
Understanding the criticality of coil handling and stamping in their process, we engaged with the team early on — right at the facility planning stage.
Instead of retrofitting or fixing post-launch issues, we worked hand-in-hand to design a customised hoisting system from the ground up, aligned with their workflow and infrastructure.
Here’s what we integrated into their facility:
- Rope Hoist and Crab Hoist configurations on both single and double girder cranes
- Low FEM Crab Hoist designed for durability and reduced wear over time
- Smart axis inverter with Hoistron for precision control and smooth, consistent lifting
Every component was selected to meet their real-world, daily operational needs — ensuring stability, ease of use, and minimal intervention from the team.
The Results of the Installation
Because the system was installed before operations began, the transition into full-scale production was seamless:
- Zero initial downtime or last-minute adjustments
- Flawless synchronization between crane operation and stamping line
- Confident and smooth operation from day one
- Predictive maintenance enabled through Hoistron — no surprises, just planned servicing
Operators adapted quickly, and production began without the usual teething problems of a new setup. The hoists worked in the background — just as intended.
The Conclusion
By choosing to integrate Carl Stahl Craftsman’s hoisting solution during the construction phase, the manufacturer eliminated guesswork and downtime before they even began.
Our tailored crane and hoist setup brought control, reliability, and long-term efficiency into their workflow — right from the start. With smooth handling, no unexpected halts, and complete visibility through Hoistron, the team could focus entirely on output and innovation, not operational hurdles.
Smart planning paid off. The crane didn’t get in the way — it quietly empowered every lift.